Senior Quality Engineering Manager
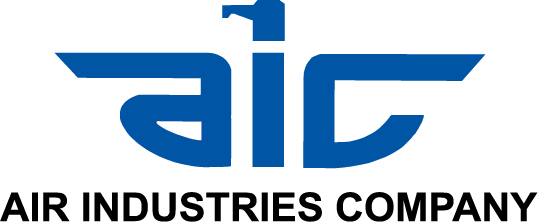
4197
With more than 120 operations and approximately 20,000 employees worldwide, Precision Castparts Corp. is the market leader in manufacturing large, complex structural investment castings, airfoil castings, forged components, aerostructures and highly engineered, critical fasteners for aerospace applications. In addition, we are the leading producer of airfoil castings for the industrial gas turbine market. We also manufacture extruded seamless pipe, fittings, and forgings for power generation and oil & gas applications; commercial and military airframe aerostructures; and metal alloys and other materials for the casting and forging industries. With such critical applications, we insist on quality and dependability – not just in the materials and products we make, but in the people we recruit.
PCC is relentless in its dedication to being a high-quality, low-cost and on-time producer; delivering the highest value to its customers while continually pursuing strategic, profitable growth.
In 2016, Berkshire Hathaway, led by Chairman and CEO Warren E. Buffett, acquired Precision Castparts Corp.
SPS Technologies, LLC dba Cherry Aerospace
POSITION AVAILABLE
Position: Senior Quality Engineering Manager
Location: Santa Ana, CA
Duties:
- Responsible for day-to-day operations of Quality Department. Manage and oversee all inspections of parts, investigate non-conformances, initiate, implement, and coordinate corrective and preventative actions (Maintaining AS9100 and NADCAP compliance)
- Interface with inspection and manufacturing personnel to support business operations: Manufacturing Engineers on technical issues, specification requirements, inspection methods and scheduling.
- Collect, organize, and analyze data; summarize findings and present recommendations from appropriate data sources.
- Design and implement training programs to all quality personnel including cross-training.
- Optimize equipment availability, cycle times, and project plans for overall better cost/budget management. Coordinate with manufacturing operations and create strategic support schedules for Inspection team.
- Monitor key business performance metrics to ensure the business can achieve uniformity across all operational areas.
- Oversee technical operations management systems and processes implemented at various production stages including labor, equipment, machinery, and supply requirements to achieve departmental productivity and meet and exceed productivity targets
- Oversee and monitor Gauge Inventory and Calibration cycles to ensure supply will meet operational demand.
- Participate in supplier selection process and provide support to purchasing department on quality and production related issues.
- Implement and facilitate production corrective and preventative action for products and systems.
- Monitor changes in Production Department and review proposed changes that may lead to unintended effects on interchangeability, documentation, certification, and functionality.
- Lead and advise teams on identified key issues in need of corrective action.
- Assess and calibrate new equipment; performing ‘in-field’ quality process audit of raw material or component supplier.
- Supervise and manage a team of 20 - 25 Inspectors and Engineers and one Supervisor.
Travel: Approximately 20% domestic travel.
Education: Bachelor's degree in Mechanical Engineering, or closely related field (foreign equivalent accepted); and
Experience: 10 years post-bachelor’s progressive experience as a Forging/Heading Production Engineer, Mechanical Engineer, or similar position
Skills/Requirements:
- Leading a minimum of 10 Six Sigma projects that materialized into measurable savings and improvements
7 years’ experience in each of the following:
- Using AutoCAD and Solidworks for 2D and 3D parts and assemblies design of new tooling for shop floor trials to test the capability and repeatability of parts; reviewing customer drawings and specifications and understanding the manufacturing steps involved to make the part to print;
- Applying knowledge of Material Science to analyze metal alloy structures and properties of formed and machined components including Mechanical Testing of such properties;
- Applying knowledge of Aerospace special processes including Heat Treatment, Nondestructive Magnetic Particle Inspection and Fluorescent Penetration Testing;
- Solving in-process defects and customer product returns through material review board (MRB) process;
- Training employees on vendor-related quality improvements and changing customer requirements;
- Identifying, validating, and implementing a prioritized list of vendor quality improvement actions, including partnering with vendors to develop specification enhancements;
- Developing models to estimate vendor-related costs of poor quality;
- Assessing vendor process controls, specification and flow down requirement compliance, and adherence to corrective actions;
- Leading cross-functional vendor quality management system activities;
- Conducting routine announced and unannounced on-site vendor visits;
- Working with Sales Team to support Request for Quote initiatives; and
- Interviewing and hiring new employees.
All experience, skills, and requirements may be gained concurrently.
This requisition is closed to applications.